The Industrial Clutch combination Rotary Seal & QRV (Quick Release/Exhaust Valve) offers the ability to tune the clutch engagement to meet each presses unique requirements. The Industrial Rotary Seal & QRV is a modular design to fit the complete range of Industrial Clutches used on mechanical stamping presses and many Verson clutches. The Poppets are a standard part across all configurations with adjustable orifices and there are various cap’s providing several air inlet options.
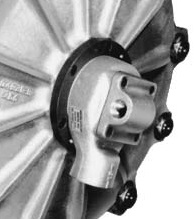
Integrating the QRV into the Rotary Union allows am Industrial Clutch the unique ability to more rapidly exhaust the clutch to reduce “Overlap” with the brake setting during the press stopping, than any other approach. This operational feature significantly improves press operation by reducing heat in the clutch and brake, while limiting unnecessary wear on the friction material and other parts.
In addition, the poppet orifice diameter can be adjusted by drilling them to a different diameter. The poppet orifice controls the engagement of the clutch, the smaller the orifice the slower the clutch engages and conversely, the larger the orifice the quicker the clutch engages. Proper orifice size improves press operation by reducing “Overlap” with the brake when the press is started and providing a smoother clutch engagement. Under proper guidance, the orifice tuning can be customized to each specific press, providing optimum performance. The standard for Industrial Clutches is:
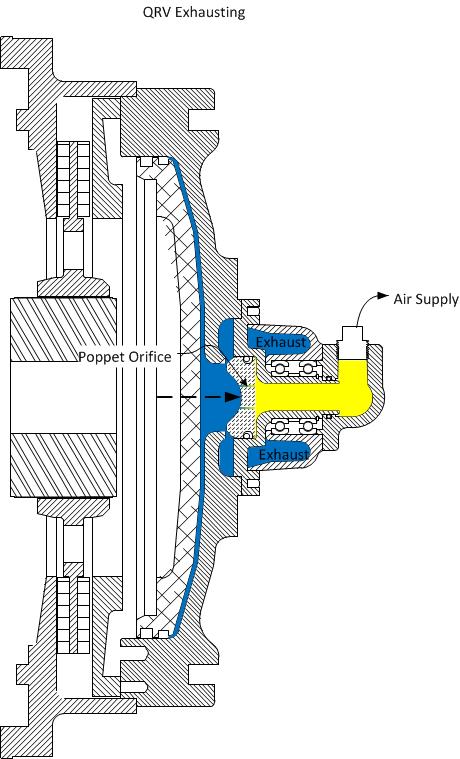
The operating principle is simple in concept, but often misunderstood, leading to most operating issues.
- When the clutch is engaged, the supply pressure is higher than the pressure in the clutch, the pressure differential moves the poppet in the rotary union to block the exhaust port while the orifice meters the air to the clutch:

- When the clutch is disengaged, the clutch pressure is higher than the supply pressure, the pressure differential moves the poppet in the rotary union to open the exhaust port:

A common issue Torque Inc., witnesses, on customer presses, is the QRV is not operating properly. This issue is caused by the supply pressure from the press safety valve not falling fast enough relative to the clutch pressure when the clutch disengages to create the pressure differential to move the poppet. There are two primary causes of this:
- The poppet orifice is drilled too large, allowing the clutch pressure to exhaust through the orifices at the same rate the supply pressure drops.
- The pneumatic plumbing and press safety valve are not allowing the supply pressure to drop fast enough for the QRV to react. The typical installation with this issue has the press safety valve located next to the brake with a very long line to the clutch. With a single press safety valve, the brake exhaust going through the valve prevents the clutch supply line pressure from dropping quickly enough for the QRV to move.
When working with the Industrial Clutch combination Rotary Seal & QRV, a simple check is to feel the exhaust air rushing out of the unit immediately upon the clutch releasing at the end of a stroke.
Torque Inc., Sales Engineers are available to consult with any Torque Inc., customers with questions or issues with these units. We have the expertise to assist tuning your press for optimal clutch engagement and disengagement. Please contact us with any concerns, we are happy to be of service.